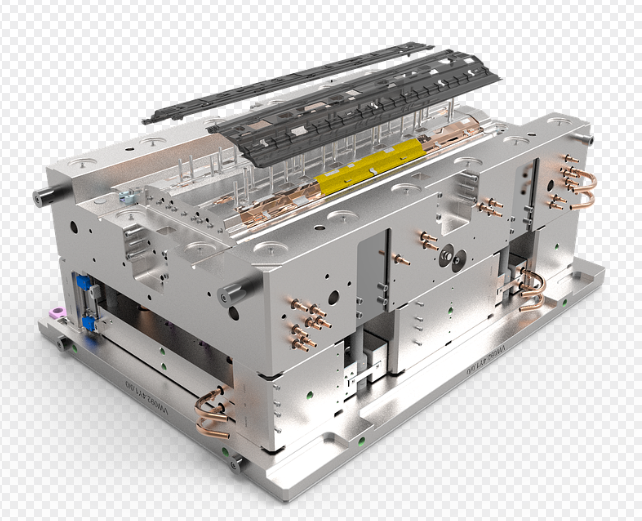
사출성형(射出成型)이란?
사출성형(射出成型)은 용해된 물질을 주형에 주입해 여러 부분을 만드는 제조 공정입니다. 주사기로 액체를 주입하는 모습과 유사하다는 점에서 「사출 성형」으로 불립니다.
사출성형은 금형을 이용한 성형법 중 하나로, 합성 수지(플라스틱) 등의 재료를 가열해서 녹이고 금형에 주입한 뒤 냉각시켜 원하는 성형을 실행합니다.
사출성형은 부품을 대량으로 생산하기 위한 공법으로, 금형과 시스템이 구비됐다면 매우 빠르고 저렴하게 생산할 수 있습니다. 사출성형은 형태와 크기에 따라 30~90초의 속도로 부품을 생산합니다. 작은 부품들은 하나의 금형을 공유할 수 있습니다.
사출성형을 위해서 필요한 하드웨어는 금형과 사출성형기로 대별됩니다. 금형(mold)을 사출성형기에 장착하여 플라스틱 제품을 생산하게 됩니다.
사출성형의 구성
사출성형은 다음과 같은 부분으로 구성되어 있습니다.
- 호퍼(hopper): 칩을 넣는 곳
- 가열통: 원료를 가열하여 녹이는 곳
- 스크루: 녹인 플라스틱을 밀어내는 곳
- 금형: 목적한 형태로 성형하는 곳
사출성형에는 가스 보조 사출 성형이라는 기술도 있습니다. 가스 보조 사출 성형은 복잡한 금형 내부에 주입된 용융된 수지 재료를 가압(가스의 압력)을 이용해 고르게 퍼지게 하는 기술입니다.
사출성형 공정
1. 충전
플라스틱 원재료를 녹여, 실린더 안으로 채워넣는 과정을 의미합니다.
사출성형의 충전은 금형을 닫고 금형 캐비티를 약 95%까지 채우는 과정입니다. 충전은 사출 주기의 첫 번째 단계로, 1차 사출에 해당합니다.
충전은 가열실린더를 통해 용융된 플라스틱이 사출압력과 속도에 의해 성형기의 노즐 구멍을 통과하면서 금형 내부로 주입되어 성형품을 형성하기 위해 채워지는 것을 말합니다.
충전 불균형은 부적절한 사출 성형 공정에 의해 발생되며, 성형 공정 조건 중 사출속도는 충전에 영향을 주는 매우 중요한 요소입니다.
사출성형에서 충전 부족현상을 해결하는 방법
충전 부족 현상을 해결하기 위해서는 다음과 같은 방법을 시도할 수 있습니다:
- 게이트가 응고되기 전에 수지가 역류하는 것을 방지하기
- 금형온도·수지온도·사출압력과 속도를 높여 충전시킨다
2. 사출
사출(射出)은 사출성형이라는 플라스틱 성형 방식의 하나입니다. 사출성형은 용해된 물질을 주형에 주입시켜 여러 부분을 만드는 제조 공정입니다. 실린더를 밀어 넣어 금형 안을 녹은 플라스틱으로 채워넣습니다.
사출성형은 금형을 이용한 성형법 중 하나로, 합성 수지(플라스틱) 등의 재료를 가열해서 녹이고 금형에 주입한 뒤 냉각시켜 원하는 성형을 실행합니다. 주사기로 액체를 주입하는 모습과 유사하다는 점에서 「사출 성형」으로 불리게 되었습니다.
3. 보압
보압은 사출 성형 공정에서 수지가 냉각 수축을 일으키며 발생하는 체적 수축을 보상하기 위해 수지를 더 공급해주는 공정입니다. 보압은 냉각 시 금형 내의 성형혼합물의 수축을 보상하기 위해 보압시간 동안 스크류로부터 용융쿠션에 동작하는 압력입니다. 보압은 용융수지를 압축하게 함으로써 밀도에 의존하는 품질의 특성을 결정합니다.
보압의 크기는 수축률이 좌우합니다. 보압의 크기가 클수록 캐비티 내의 압력은 비례적으로 증가하는 경향을 보입니다. 보압의 크기가 클수록 냉각 후 잔여압력도 증가합니다.
보압 시간은 게이트가 완전히 고화되는 시간(gate seal time) 이상으로 설정해야 균일한 제품을 얻을 수 있습니다.
4. 냉각
사출 성형에서 냉각은 제조 주기의 가장 큰 부분으로, 주기의 약 60-70%를 차지합니다. 냉각 시간은 플라스틱 제품의 성형 사이클 길이와 출력에 직접적인 영향을 미칩니다. 냉각 시간을 약간 줄이면 생산 작업에서 더 짧은 시간에 더 많은 제품을 생산할 수 있습니다.
사출 성형 냉각 시스템 구성
- 고압 하에서 용융 된 중합체를 차가운 금속 주형으로 강제합니다.
- 캐비티에 충전이 완료되면 빠른 냉각이 시작됩니다.
- 금형내로 유입되는 냉각수가 냉각채널을 통하여 캐비티의 열을 빠르게 방출시킵니다.
사출 성형 냉각 시스템 설계 시 고려사항
- 제품 두께는 가능하면 일정하게 해야 합니다.
- 냉각수로의 최적 위치는 금형 캐비티와 코어를 가지고 있는 블록(block)입니다.
- 냉각수 온도는 5 ℃ 이상인 경우가 많습니다.
- 온도 차이가 작을수록 동일한 양의 열을 배출하려면 더 높은 유량의 냉각수가 필요합니다.
5. 이형
사출 성형 제품은 성형과 경화 후 금형 캐비티나 코어에서 꺼내는 것을 이형이라고 합니다. 성형 수축 등으로 인해 플라스틱 부품이 코어를 감싸거나 금형 캐비티에 갇히는 경우가 있습니다.
사출성형 이형 공정이 어려울 때 시도할 수 있는 방법
- 사출 압력을 낮추면 사출 시간이 단축되고 용융물과 금형의 온도가 낮아져 탈형이 쉬워집니다.
- 플라스틱과 금형 사이의 마찰을 줄이는 이형제를 사용합니다.
- 나노 이형 코팅을 사용합니다. 플라스틱 몰드의 표면이나 플러그인 표면에 코팅을 형성해 마찰 계수를 줄이고 고광택 처리 표면을 얻을 수 있습니다.
사출성형 불량의 원인
사출 성형 불량의 원인으로는 다음이 있습니다.
- 충전 부족 (Short Shot)
- 흑줄 (Black streak)
- 크랙 (Crack)
- 플래시 (Flash, Burr)
- 플로우 마크 (Flow Mark)
- 젯팅 (Jetting)
다음 글에서 사출성형 불량의 원인에 대해 자세히 설명하겠습니다.
마무리
오늘은 플라스틱 사출성형(射出成型) 공정, 구성, 불량의 원인에 대해 알아보았습니다.
사출성형의 공정을 조금 더 간단하게 정리하자면 아래와 같습니다.
- 가소제, 충전제 등을 첨가하여 원통형 또는 원형으로 된 수 mm 의 칩(chip 또는 pellet)을 호퍼에 넣는다.
- 투입된 재료는 가열실린더에서 재료에 따라 알맞게 가열하여 재료를 용융상태로 만든다.
- 이것을 스크류로 투입구를 통해서 금형(金型) 속으로 사출한다.
- 냉각된 제품을 금형에서 꺼낸 뒤, 표면 마감 등 후공정을 거쳐 복잡한 3차원 형상을 만듭니다.